PREFABRICATION. IS IT A FIT FOR YOUR HEALTHCARE PROJECT?
“Speed, quality, and cost benefits are all intertwined through the prefabrication process, all while improving patient care. That’s a huge benefit for everyone involved.”
Every industry is looking for speed to market, costs savings, and to increase overall quality. One way to make that possible in project delivery is through prefabrication. It’s a technique where all the components are built offsite under a controlled construction environment and then assembled on site.
We recently sat down with MSKTD’s Healthcare Design team and asked them to share their take on prefabrication, based on their experience.
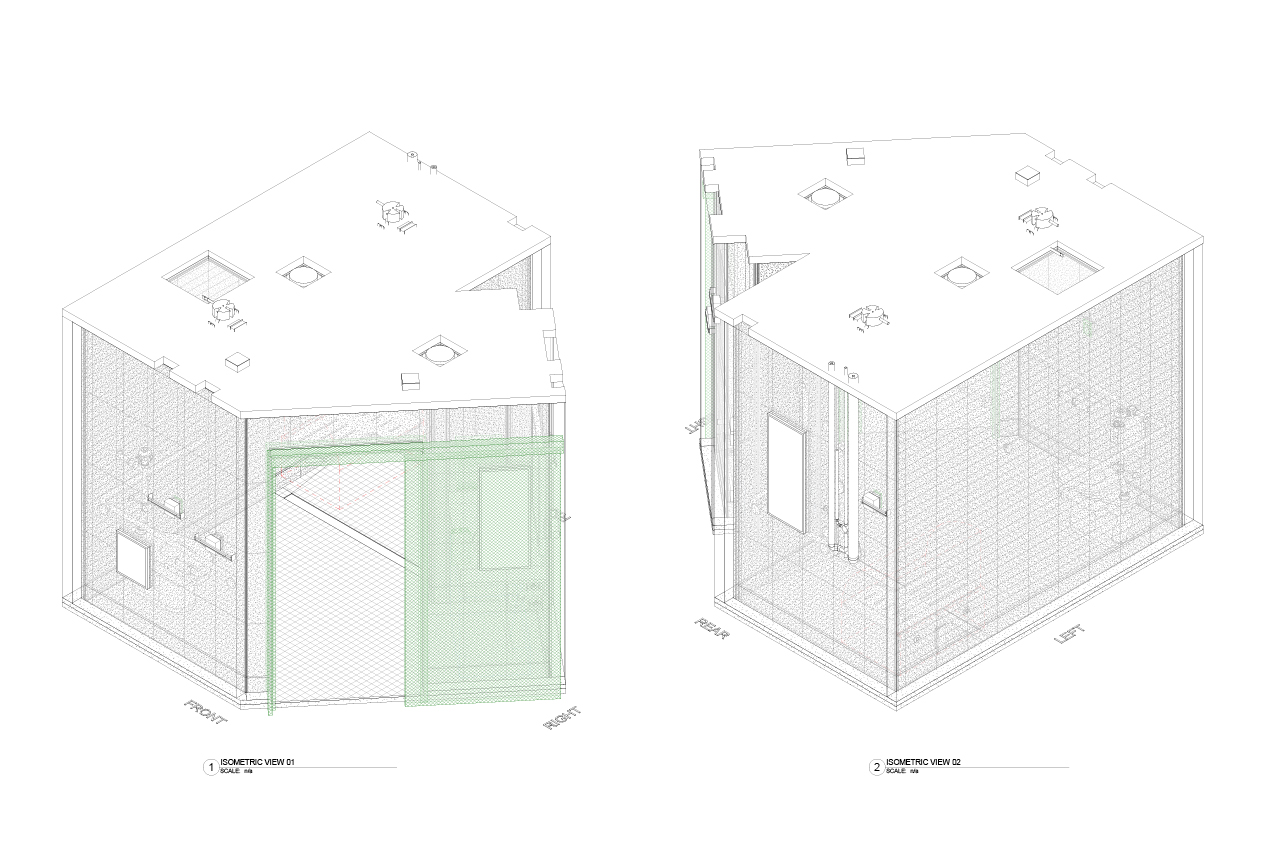
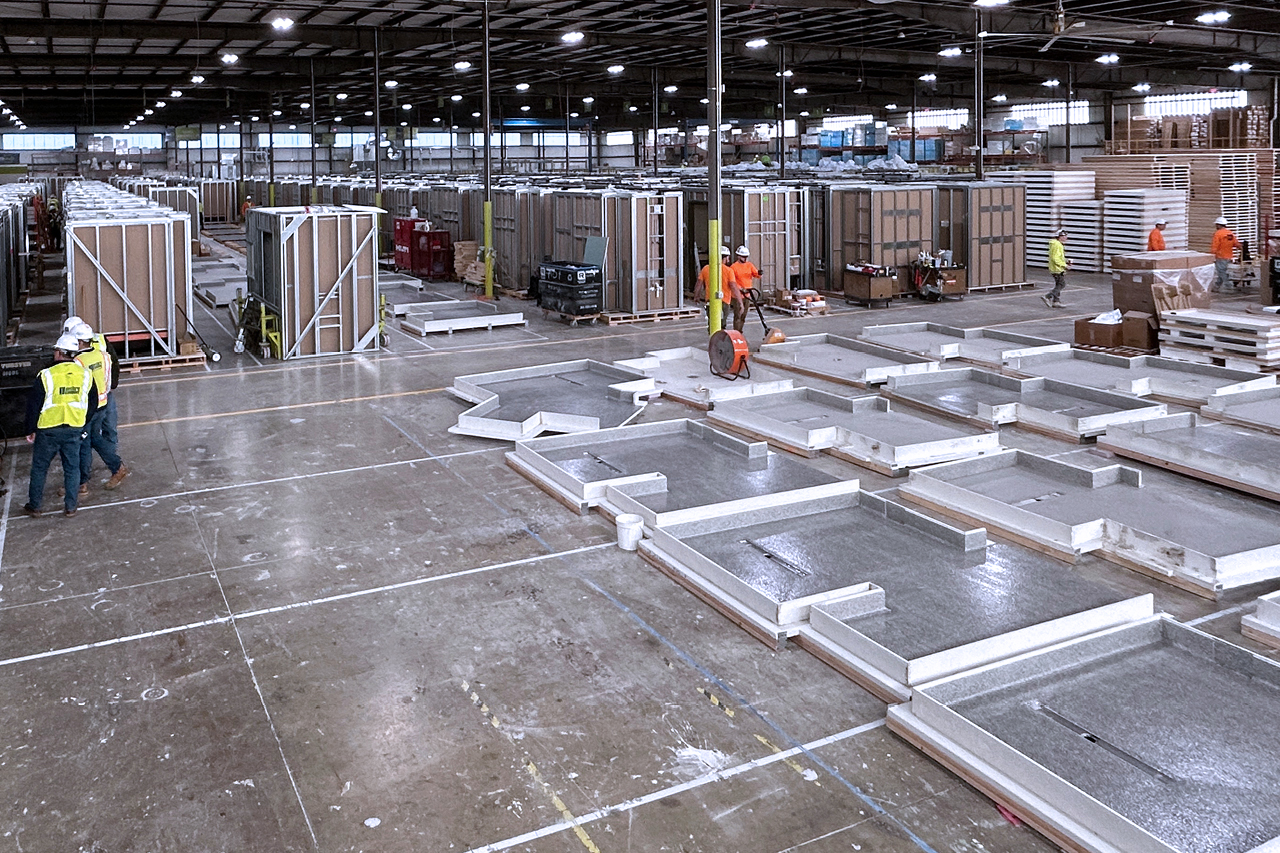
WHAT ARE THE MAIN BENEFITS OF PREFABRICATION?
The single greatest benefit of prefabrication to our healthcare clients is the ability to significantly reduce disruptions to their operations and ultimately to patient care.
In a traditional build all construction activity is done onsite. With prefabrication, the modules are constructed off site and shipped to the location ready to install when they arrive. This means the overall time spent on site is reduced with significantly less noise, debris, dust, and cleanup.
WHEN IS PREFABRICATION THE RIGHT OPTION FOR A CLIENT?
Project size, type, and budget are major factors in considering whether prefabrication is a value add. Projects that make use of repetitive interior and exterior elements usually see the most benefit.
In the healthcare industry, prefabrication inherently lends itself to room standardization. Healthcare professionals often move from room to room and even between buildings to treat patients. With standardized treatment modules, these providers no longer need to re-orientate to the room, regardless of location.
A building’s exterior façade, mechanical/electrical/plumbing (MEP) components, and anything above the ceilings, such as sprinkler systems, plumbing, ductwork, telecommunications, and electrical systems can also be prefabricated. Instead of bringing individual pieces of conduit, for example, contractors can slide pre-assembled racks in place and hook them together on site.
WHAT OTHER FACTORS NEED TO BE CONSIDERED WITH PREFABRICATION?
If prefabrication is a viable option, it’s important to ensure the project’s entire team—the designers, engineers, construction, and especially the client, are all aligned early in the process. All future decisions will revolve around planning for the use of prefabrication. The client needs to specifically be aware that although prefabrication can offer significant cost savings and many other benefits in the long run, unlike a traditional build, there is an upfront investment (for design and engineering, tooling and equipment manufacturing, facility setup, and materials purchasing).
The team also has to give careful consideration to installation, especially when adding onto an existing building. Since pre-assembled units are being installed, we need to plan for an opening large enough in the building to move those modules into place.
IS PREFABRICATION A SUSTAINABLE OPTION?
While sustainability isn’t the driving factor in determining whether prefabrication is the right fit for a project, it’s a benefit worthy of consideration. In addition to cutting down on waste at the project site, prefabrication offers contractors the ability to make building materials to spec, which cuts back on a project’s waste as a whole. This results in less product ending up in landfills; and fewer materials needing to be transported to the building site, reducing freight and emissions. Prefabricators are constantly seeking innovations in process and products to improve a project’s overall environmental footprint.
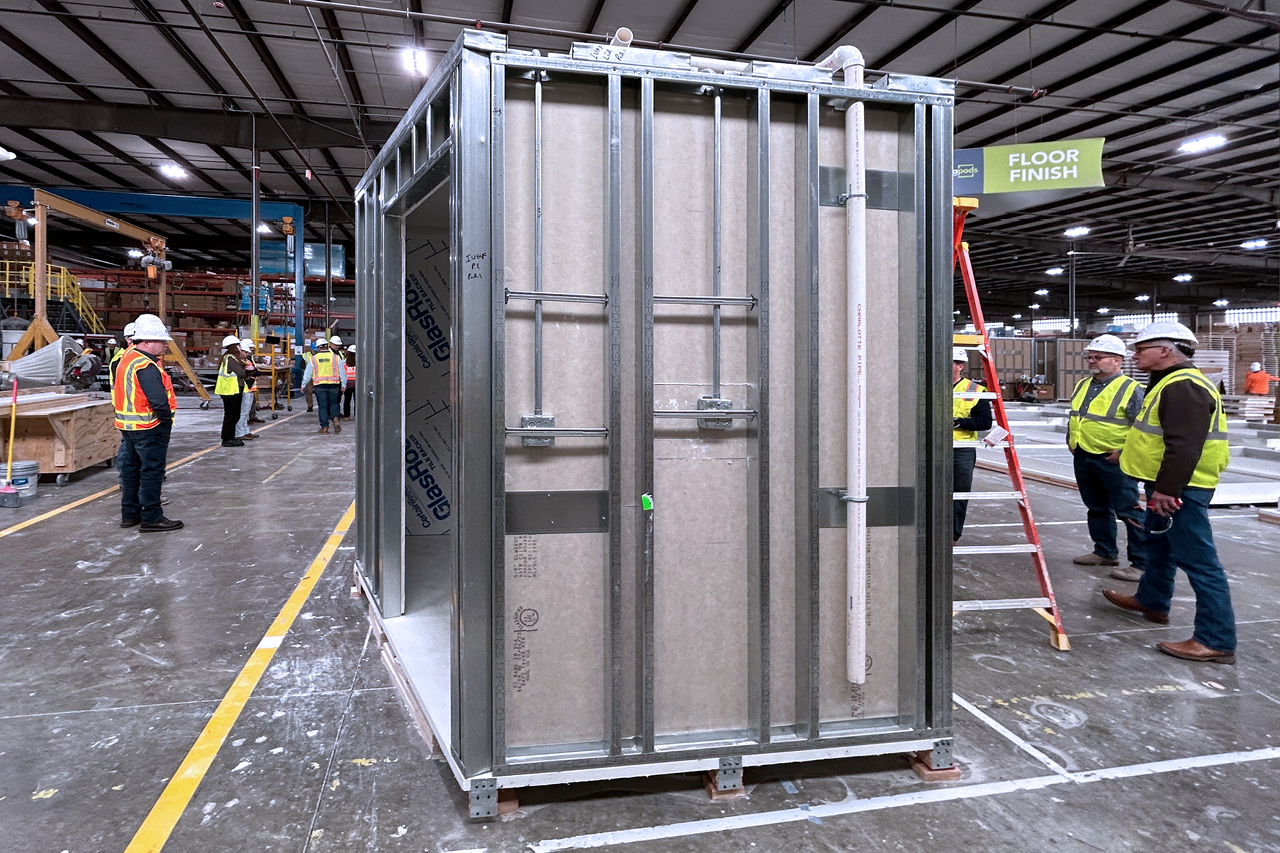
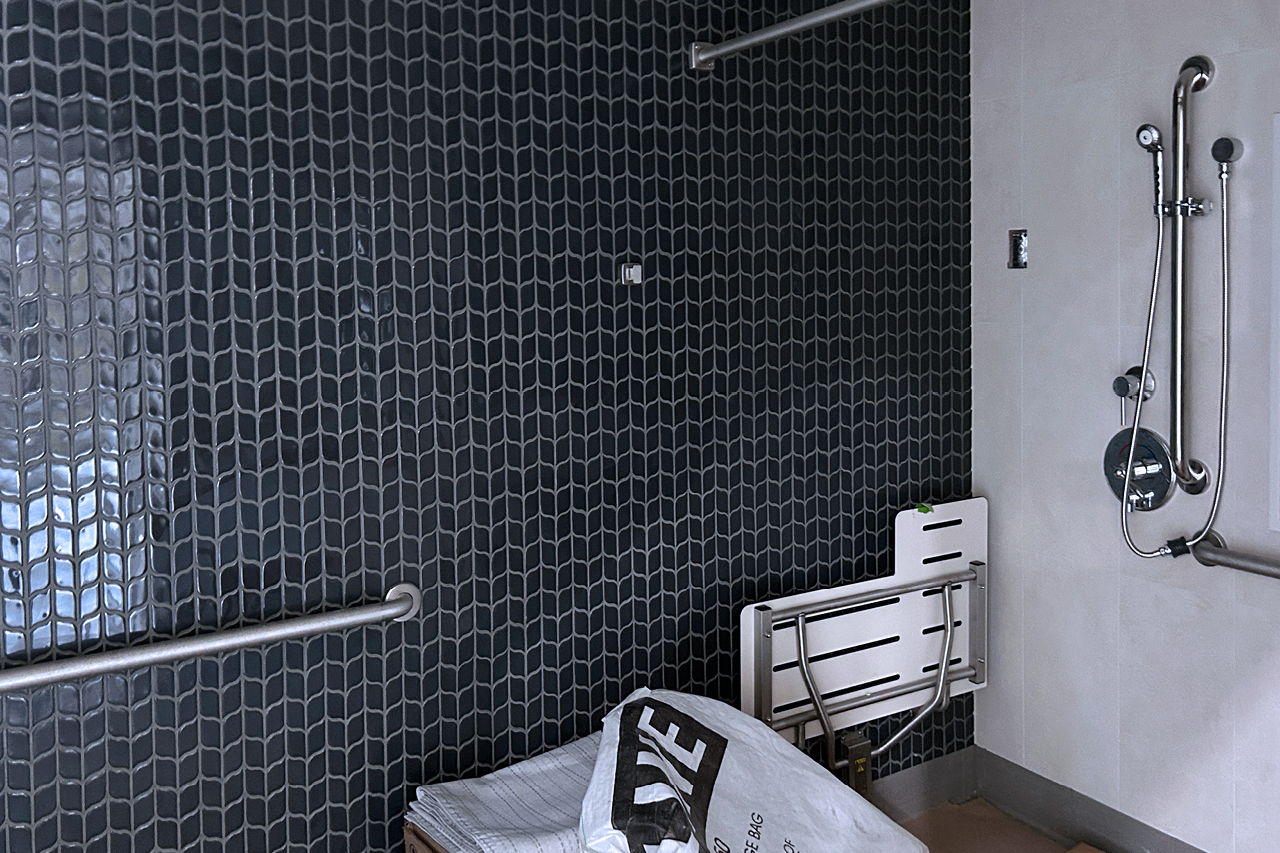
WHAT ARE SOME MISCONCEPTIONS ABOUT PREFABRICATED ROOMS AND FAÇADES?
Prefabrication is not a good choice for someone looking for unique customization from room to room. There is a certain volume and standardization needed for prefabrication to be an economical design solution. But just because prefabricated modules are standardized, doesn’t mean that they are lower in overall quality or must be boring. In fact, it is quite the opposite. Prefabrication has proven to improve the quality of workmanship in construction. It increases uniformity of the fit and finish of the rooms where it is applied. As with all healthcare projects, we only use materials that are appropriate and meet the healthcare industry standards. Our design team works closely with our clients to provide commercial-grade options for finishes and color schemes that complement the overall building or desired aesthetic for both the interior rooms and exterior façades.
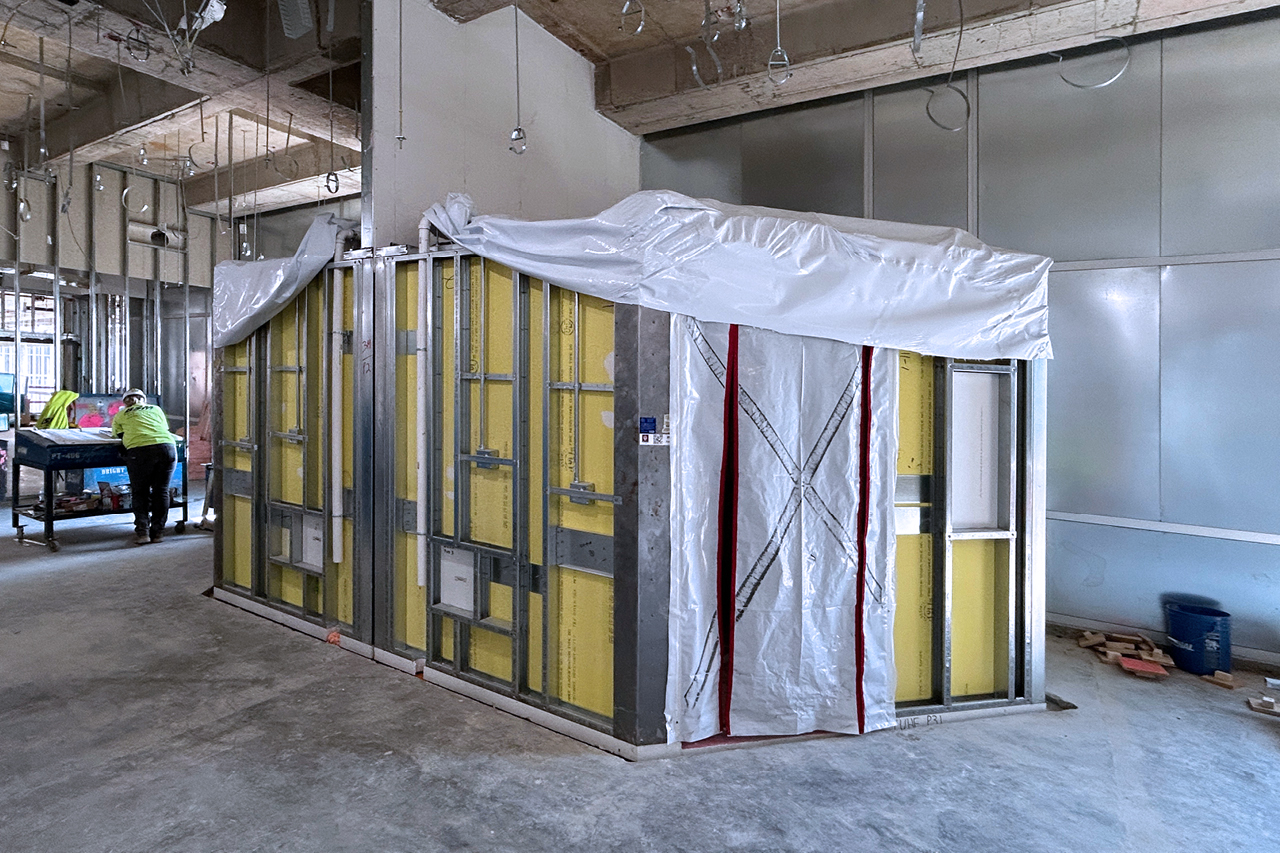
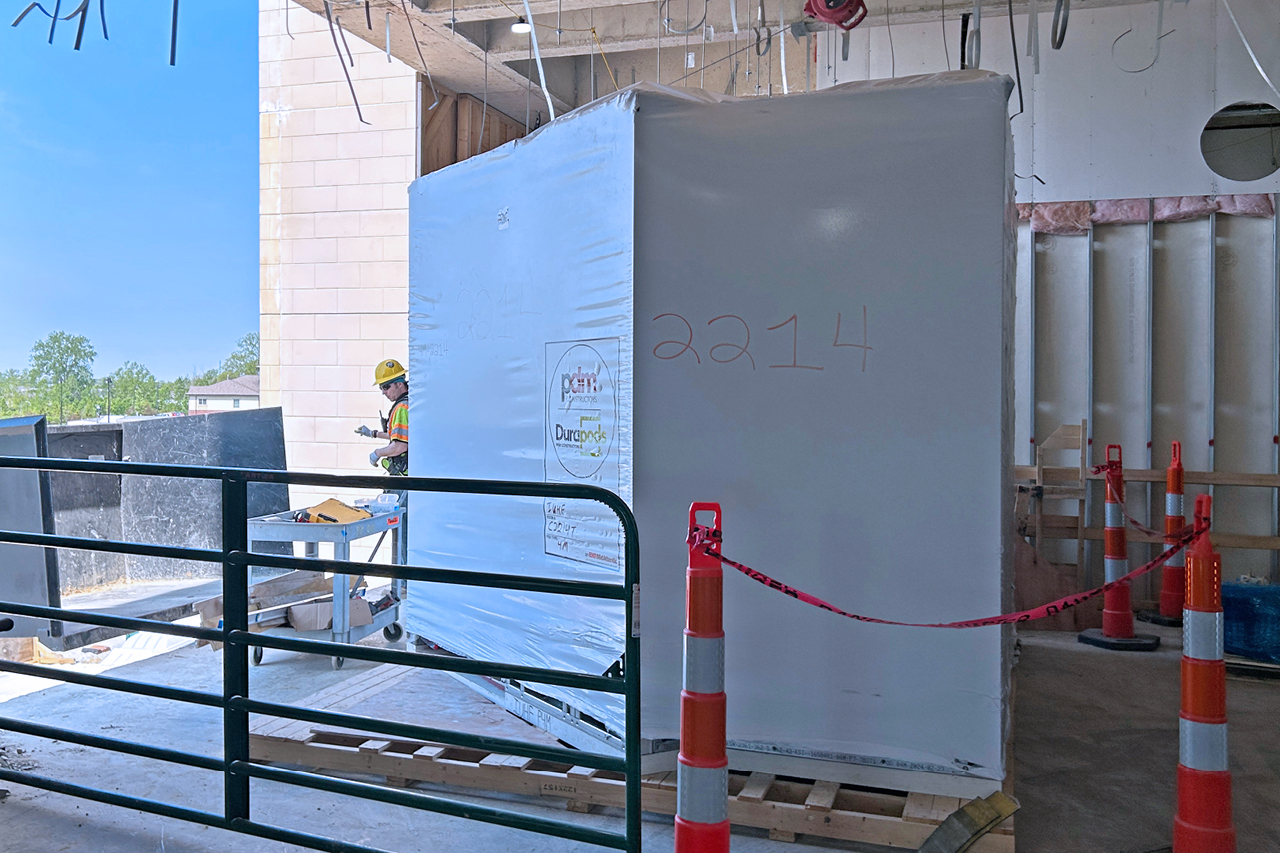
WHAT ARE LESSER-KNOWN BENEFITS OF PREFABRICATION?
When working with healthcare systems that manage medical facilities across multiple locations, we can create a prototype pod or module of any room type (think exam room, lab, or bathroom.) The prototype module can be transported to various locations within the healthcare system, allowing clinical team members from the multiple locations to provide feedback on the fit-out of a room. This extra step allows us to gather real-time data on how different teams will need to move around and utilize the space. Using a prefabricated module in this manner provides invaluable information enabling our design team to make important adjustments to the interior layout before finalizing and constructing a standardized room type.
With everything being built offsite, this also means quality control is enhanced, safety is improved, and we can keep a project moving. The impact of seasonal elements on timelines and on the materials themselves is significantly reduced.
And because prefabrication is modular in nature, this process can accommodate future updates.
OUR SOLUTIONS ARE NOT PREFABRICATED
As a full-service A/E firm for over 46 years, MSKTD has seen the use and acceptance of prefabrication increase across all our markets. Because of the many benefits of prefabrication, it has become more widely known and accepted. In turn, our clients are more frequently asking us if they should be incorporating it into their projects. Although it may not be the right solution for every project, we actively ask questions and actively listen to fully understand and find the right solutions for each particular project.